How is tyre to oil recycling pyrolysis process ?
Waste Tire/Plastic Pyrolysis Plant / Date:April 25, 2018
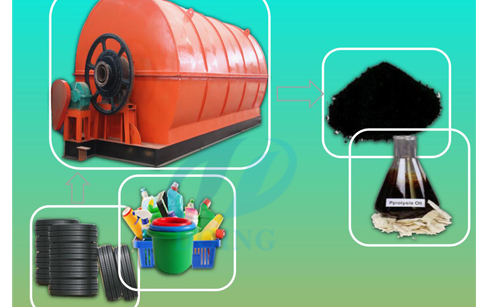
Waste tyre to oil recycling pyrolysis process
The pyro-gas generated form pyrolysis process is used as fuel in the pyrolysis process. In these plants the full tyres are fed to the pyrolyser manually and at the end of the process the steel wire and carbon are taken out manually. This leads to lot of carbon spillage, exposure of workers to fine carbon particles and working in the unconducive environment in the pyrolyser.
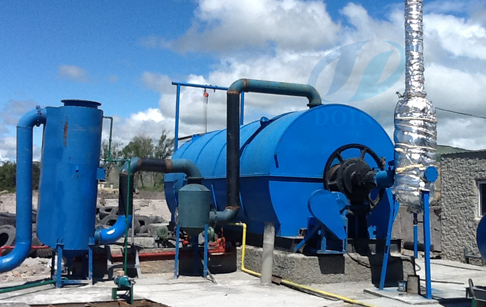
Waste tyre to oil recycling pyrolysis process plant
Batch process:
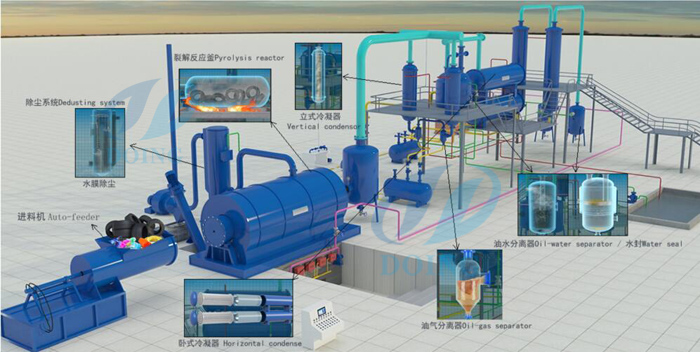
Waste tyre to oil recycling pyrolysis process
1.The feed to the pyrolysis reactor should be devoid of steel. After removal of steel wire the tyre can be put either in the form of crumbs or chips (which can be made simply by cutting without going for the shredding process).Further the feeding arrangement of the rubber crumb to the reactor should be mechanised.
2.The initial heating of the reactor should be done by liquid fuel or gas. The flue gas should be released to the environment through a chimney of at least 30 metres height
3.After initial heating, during the pyrolysis process, the pyro gas generated within the plant should be used as a fuel.
4.Excess pyro gas if any should be flared through properly designed flaring system of adequate capacity considering the emergency situation in which the entire gas may have to be flared. The flaring should be done at a minimum height of 30 metre.
5.Adequate instrumentation for measurement and control of temperature and pressure along with safety interlocks in case of increase of temperature or pressure to cut off heating of the reactor should be provided. Automatic control systems such as Programmed Logic Control (PLC) shall be adopted. It should be ensured that the reactor is under positive pressure all the time.
6.In order to control fugitive emissions from the reactor during operation, proper sealing should be ensured.
7.The collection of the oil from the condensers should be in closed vessel and storage also should be in closed tanks with suitable vents. There should be no manual handling of oil. Transfer of oil should be through pumps.
8.At the end of the pyrolysis process the reactor has to be cooled before the removal of carbon. During this process, the reactor should be purged with nitrogen.
The removal of carbon should be started after the reactor's temperature has come down to below 50°C.
9.The removal of carbon black should be through a mechanised system and it should be ensured that no spillage takes place during the collection of the carbon in the bags.
10.Adequate number of sensors along with alarm system should be provided at suitable locations throughout the plant to detect any leakage of flammable vapors from the system
Request Information
Send your inquiry for further information