Small scale waste plastic pyrolysis plant
Waste Plastic Pyrolysis Plant / Date:01-30-2021
As plastic products becomes more and more widespread, the pollution caused by plastic waste is also getting more and more serious. Waste plastic pyrolysis plant can convert waste plastic into fuel oil and carbon black, which is an environmentally friendly way to recycle and reuse resources. If you want to invest in waste plastic to fuel oil project, but worry that the investment is too big, you can buy small scale waste plastic pyrolysis plant to start this project first, and then expand your business when it is profitable.
The introduction of small scale waste plastic pyrolysis plant
Doing small scale waste plastic pyrolysis plant
Like large and medium-sized pyrolysis plant, small scale waste plastic pyrolysis plant also uses the principle of pyrolysis to recycle waste plastics, only its daily capacity is 500kg-2000kg, and it takes about 20 hours for one batch. The small scale waste plastic pyrolysis plant is designed in one frame, easy to transport, no installation, no foundation, simple operation and low cost, which is ideal for laboratory or initial exploration stage of the project. In addition, the small scale waste plastic pyrolysis plant can be used not only for waste plastics, but also for recycling waste tires, waste rubber and even waste oil sludge.
The working process of small scale waste plastic pyrolysis plant
The raw materials and products of small scale waste plastic pyrolysis plant
1. Feeding raw materials
Put the dry plastic waste into the pyrolysis reactor, the quantity should be controlled below 2/3 of the pyrolysis reactor to make it rotate more smoothly. Then close the feed door.
2. Heating pyrolysis reactor
The heating of pyrolysis reactor includes two stages: from 100℃ to 250℃ for the primary stage, light oil gas is released at 100℃ and liquid oil is released at 120℃; 280℃ to 350℃ is the highest oil output rate interval. The heavy oil are collected and liquefied in the center of the manifold and descend to the heavy oil tank. The lighter gas rises to the condensing system and then are liquefied and stored in the oil tank. The non-condensable gas after desulfurization and dedusting system will be led to the furnace to heat pyrolysis reactor to save energy costs.
3. Carbon black discharge
At the end of the process, cool the pyrolysis reactor. When the temperature drops to 50-70 degrees, the carbon black will be discharged automatically.
Depending on the quality of the plastic, the oil yield of fuel oil ranges from 40% to 90%, with the rest being carbon black and combustible gas. These products are widely used in industrial fields.
The applications of fuel oil and carbon black
▶ Fuel oil
Fuel oil has high calorific value and can be sold directly to cement plants, boiler plants, steel plants and other industrial plants. It can also be converted into gasoline or diesel through plastic pyrolysis oil distillation plant, which have a high calorific value and are more widely used in large machinery such as boats, forklifts and tractors.
▶ Carbon black
Carbon black has a calorific value similar to that of coal and can be used as a substitute for coal. It can be sold directly, or pressed into briquettes for sale, or ground and sold as raw material for rubber, pigments and other products.
▶ Combustible gas
Combustible gas is generally introduced directly into the furnace as an auxiliary fuel to heat the pyrolysis reactor, or it can be collected and sold on the market.
Doing Group is a leading global manufacturer of waste plastic pyrolysis plant, and Doing pyrolysis plants have been sold to more than 60 countries around the world and are well received in the industry. In addition, we offer large capacity pyrolysis plant, as well as highly automated continuous pyrolysis plant. If you are interested in pyrolysis plant, welcome to write down your contact information and requirements below, and we will give you a specific quote.
Prev:Nothing
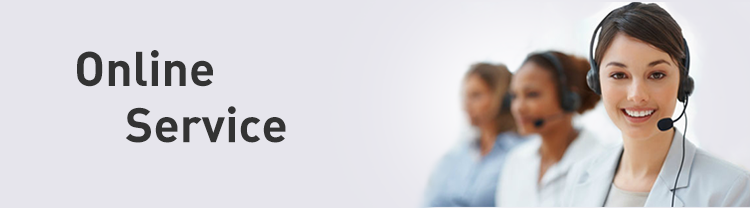