Turning waste plastic to oil machine
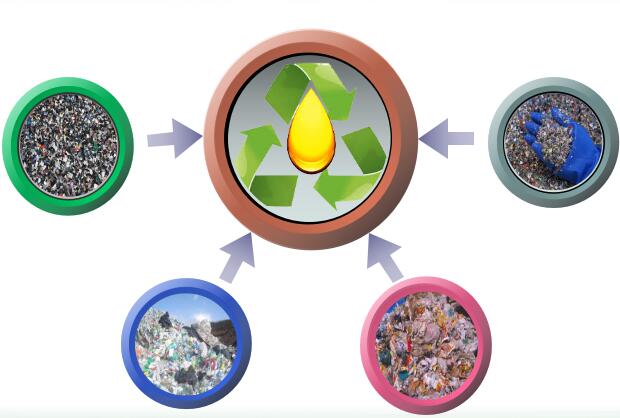
Turning plastic into oil
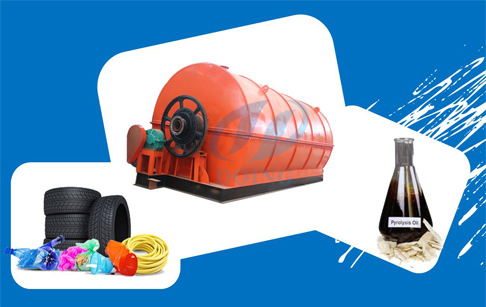
Turning plastic into oil machine
So, turning waste plastic to oil machine will have two benefits. First of all, the hazards caused due to plastic waste can be reduced and secondly, we will be able to obtain some amount of fuel oil from it, which can be further purified t o be used as a fuel in different areas such as domestic fuel, fuel for automobiles and industries etc.
Turning waste plastic to oil machine is an environmental protection system which uses the continuous liquefaction technology and catalytic breakdown reaction to convert waste plastics into renewable resources, such as pyrolysis oil, carbon black, combustible gas and so on. The end products can be applied to diesel engines and generators directly, or come into high ranking diesel and gasoline through our oil refining plant.
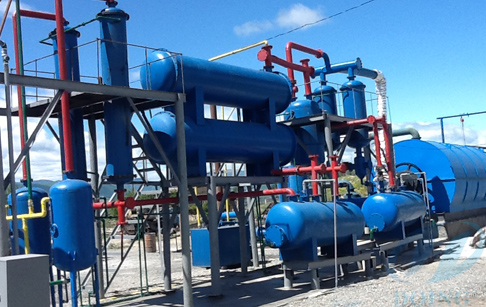
Turning plastic into oil machine
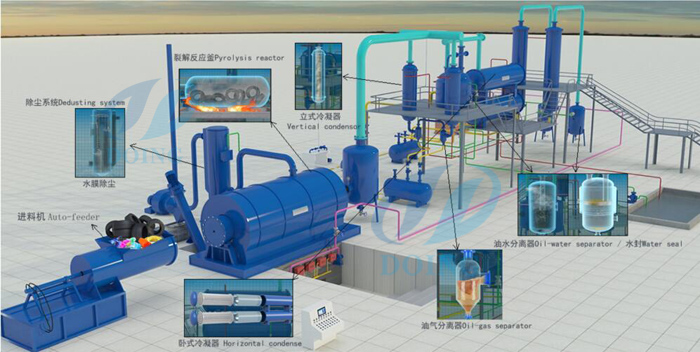
Turning plastic into oil machine working process
Turning waste plastic to oil machine process flow: plastic separation → automatic feed → catalytic cracking→ oil-water separation → cooling liquid → crude oil → flammable gas recovery → flammable gas combustion → desufuration and dust removal
Turning waste plastic to oil machine main part
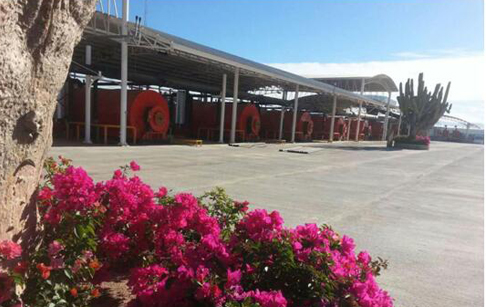
Turning plastic into oil machine
1.Heating system
Reactor
Using Q245R boiler steel and the thickness is 16mm and 18mm,the thickness would be changed according the customers'requirments. The main engine use horizontal-type of 360°structure-0.4 r/min
2.Separation system
Gas separator & Depositing tank
Depart the heavy oil and impurities from the oil gas to purify the oil.
3.Condensing system
Generally speaking , for all the raw material all be finished by heating to gasification and cracking, and then cooling to get oil, so they key is the relationship between the yield rate and condensation. So the best and easy way is to increase the condense area so as to get higher yield rate.
4.Dedusting system
Desulfurization dedusting, Water film cyclone
Desulfurization dedusting:remove the sulphur(when use coal as fuel) and dust
Water purification: for the second removal.
5.Waste gas recycles system
Water seal & Spray fire gun
In the process of refining oil, when the gas is heated up to 150 , it will produce a large amount of gasCH4& C4H8 ,which cannot convert to liquid at normal temperature and normal pressure. However, these gases can be used as fuel, which is not only environment protection but also energy conservation
6.Carbon black recycles system
The solid residual will be left after the catalyst splitting from scrap plastic, approximately take up 5% to 10% of the waste plastic.
Its main component is the black carbon, which can be used as raw materials in industry, as well could be mixed with the pulverized coal ash to produce the raw material of the thermal power plant, and also could be applied to the manufacturingof the pulverized coal ash brick (one kind of environmental protection building material)
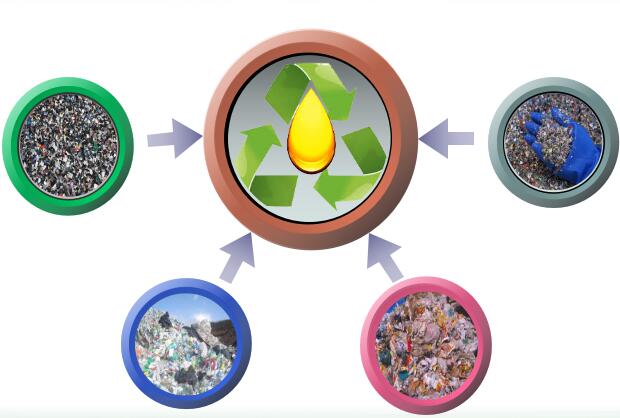
Turning plastic into oil
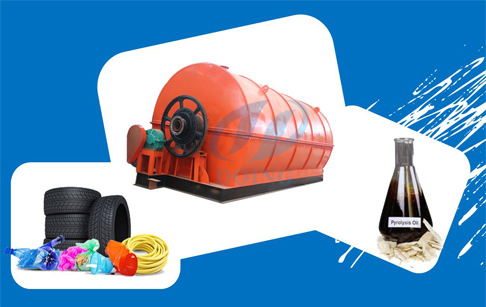
Turning plastic into oil machine
So, turning waste plastic to oil machine will have two benefits. First of all, the hazards caused due to plastic waste can be reduced and secondly, we will be able to obtain some amount of fuel oil from it, which can be further purified t o be used as a fuel in different areas such as domestic fuel, fuel for automobiles and industries etc.
Turning waste plastic to oil machine is an environmental protection system which uses the continuous liquefaction technology and catalytic breakdown reaction to convert waste plastics into renewable resources, such as pyrolysis oil, carbon black, combustible gas and so on. The end products can be applied to diesel engines and generators directly, or come into high ranking diesel and gasoline through our oil refining plant.
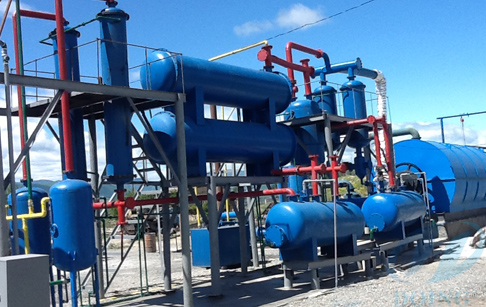
Turning plastic into oil machine
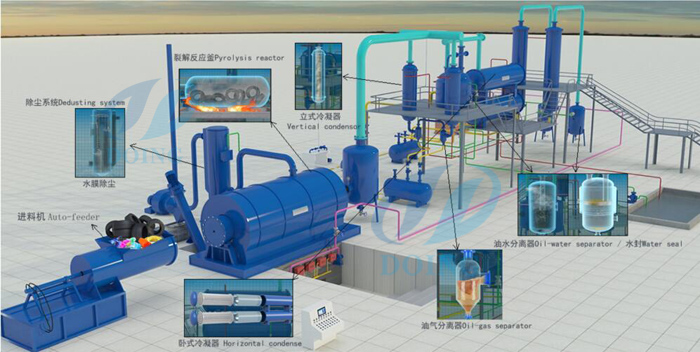
Turning plastic into oil machine working process
Turning waste plastic to oil machine process flow: plastic separation → automatic feed → catalytic cracking→ oil-water separation → cooling liquid → crude oil → flammable gas recovery → flammable gas combustion → desufuration and dust removal
Turning waste plastic to oil machine main part
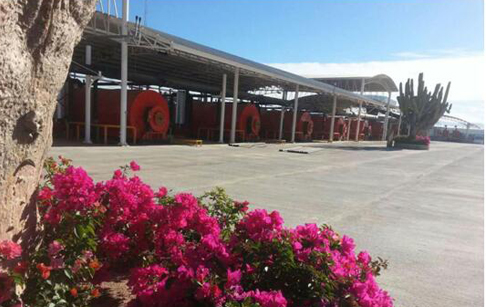
Turning plastic into oil machine
1.Heating system
Reactor
Using Q245R boiler steel and the thickness is 16mm and 18mm,the thickness would be changed according the customers'requirments. The main engine use horizontal-type of 360°structure-0.4 r/min
2.Separation system
Gas separator & Depositing tank
Depart the heavy oil and impurities from the oil gas to purify the oil.
3.Condensing system
Generally speaking , for all the raw material all be finished by heating to gasification and cracking, and then cooling to get oil, so they key is the relationship between the yield rate and condensation. So the best and easy way is to increase the condense area so as to get higher yield rate.
4.Dedusting system
Desulfurization dedusting, Water film cyclone
Desulfurization dedusting:remove the sulphur(when use coal as fuel) and dust
Water purification: for the second removal.
5.Waste gas recycles system
Water seal & Spray fire gun
In the process of refining oil, when the gas is heated up to 150 , it will produce a large amount of gasCH4& C4H8 ,which cannot convert to liquid at normal temperature and normal pressure. However, these gases can be used as fuel, which is not only environment protection but also energy conservation
6.Carbon black recycles system
The solid residual will be left after the catalyst splitting from scrap plastic, approximately take up 5% to 10% of the waste plastic.
Its main component is the black carbon, which can be used as raw materials in industry, as well could be mixed with the pulverized coal ash to produce the raw material of the thermal power plant, and also could be applied to the manufacturingof the pulverized coal ash brick (one kind of environmental protection building material)
Fuel oil (45% to 50%) of turning waste plastic to oil machine
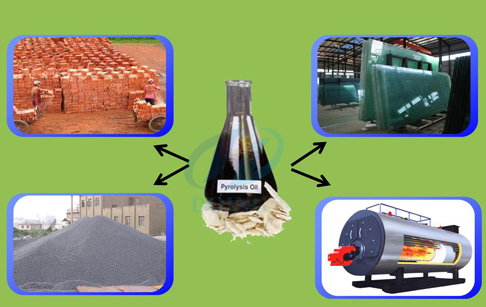
Fuel oil application
Carbon black (30% to 35%) of turning waste plastic to oil machine
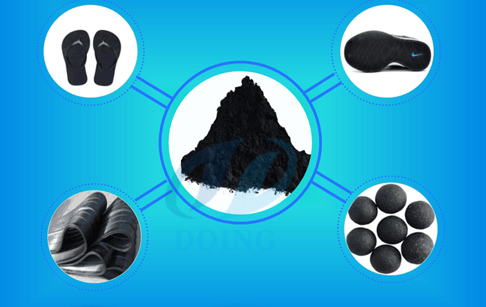
Carbon black application
Carbon black produced by Pyrolysis process (CBp) is more economical compared to carbon black produced primarily from petroleum and is more price-efficient to be used as an ingredient in the industries listed;
Electric cable jacketing
Conveyor band
Carrier Bands
Black nylon bag, Plastic pipes
Rubber additive
Automotive spare parts
Black colorant in rubber materials
Industrial rubber products
Request Information
Send your inquiry for further information