Mechanical conversion of plastic into fuel
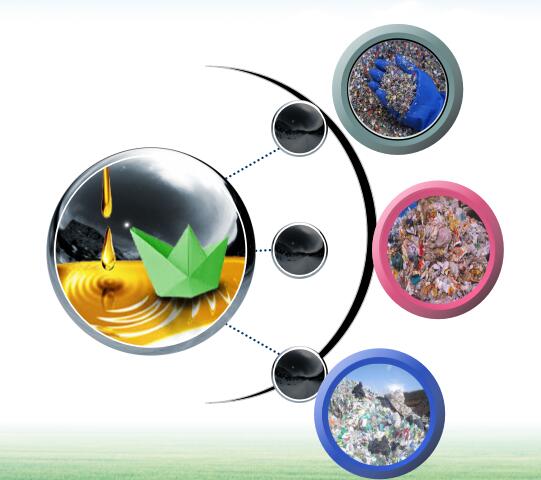
Plastic in to fuel
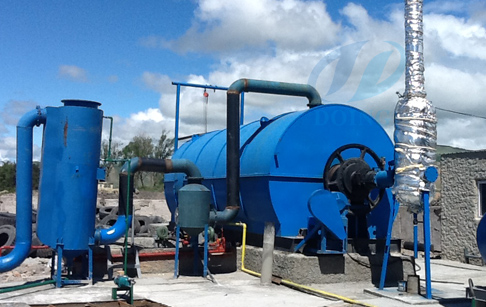
Mechanical conversion of plastic into fuel
Mechanical conversion of plastic into fuel adopts the pyrolysis technology to achieve the plastic waste to fuel oil conversion. The mechanical conversion of plastic into fuel is a chemical process of breaking down large molecules of plastic into smaller molecules of oil, gas and carbon black. The following is the details about how to get fuel oil from plastic waste.
Mechanical conversion of plastic into fuel working process
Mechanical conversion of plastic into fuel working process
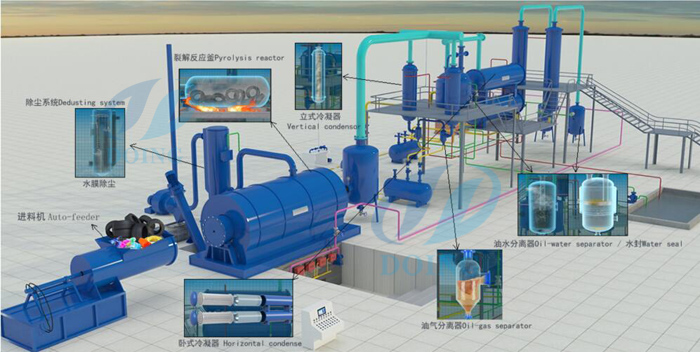
Mechanical conversion of plastic into fuel working process
Step -1
Put plastic material into the pyrolysis reactor by mechanical feeding machine or manual, then it is delivered into the store bin with the help of conveyor belt. Then, close the feeding door and open heating system of the machine.
Step – 2
In this step, two stages are there in the process. The primary stage: the heat energy needs to start with 100 degree Celsius and ending with 250 degree Celsius. In 100 degree Celsius, the oil gas will release and in 120 degree Celsius the liquid oil will release. The secondary stage: the heat energy needs to change from 250 degree Celsius towards 280 degree Celsius; it is the peak output rate. The oil gas will be collected into the manifold, and the oil as well as the weighty particles are accumulate and dissolved in the center of the manifold and drop into the deep oil container (oil tank). And the lighter oil gas will certainly go up to multifunctional oil condensers to liquefy into oil and keep in the tank.
Step – 3
Cool down the plastic to oil conversion plant after the completion of Step-1 and Step-2. Once the heat reaches about 40 degree Celsius, the carbon black will be discharged automatically.
Mechanical conversion of plastic into fuel advantage
Put plastic material into the pyrolysis reactor by mechanical feeding machine or manual, then it is delivered into the store bin with the help of conveyor belt. Then, close the feeding door and open heating system of the machine.
Step – 2
In this step, two stages are there in the process. The primary stage: the heat energy needs to start with 100 degree Celsius and ending with 250 degree Celsius. In 100 degree Celsius, the oil gas will release and in 120 degree Celsius the liquid oil will release. The secondary stage: the heat energy needs to change from 250 degree Celsius towards 280 degree Celsius; it is the peak output rate. The oil gas will be collected into the manifold, and the oil as well as the weighty particles are accumulate and dissolved in the center of the manifold and drop into the deep oil container (oil tank). And the lighter oil gas will certainly go up to multifunctional oil condensers to liquefy into oil and keep in the tank.
Step – 3
Cool down the plastic to oil conversion plant after the completion of Step-1 and Step-2. Once the heat reaches about 40 degree Celsius, the carbon black will be discharged automatically.
Mechanical conversion of plastic into fuel advantage
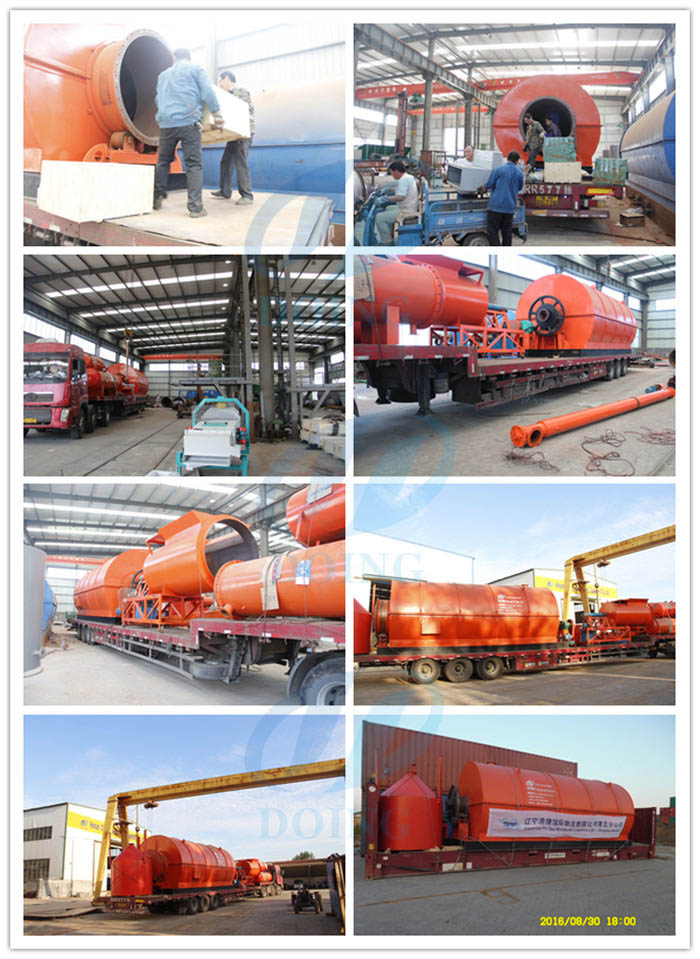
Mechanical conversion of plastic into fuel will be delivery
1. Turning waste into wealth
The mechanical conversion of plastic into fuel has introduced the newest pyrolysis technology, which can convert waste plastic to oil, carbon black and a little combustible gas. All the final products are very useful and have wide applications. By investing in the plastic recycling pyrolysis plant, our customers can profit much from processing waste plastics; at the same time, it can also reduce waste plastic pollution as well as make contribution to the environment.
2. Safe and environment friendly
The mechanical conversion of plastic into fuel is equipped with mature safety devices (alarm for over temperature and pressure, auto pressure releasing system, extra gas recycling system, fire fighting devices) and advanced dedusting system (dust chemical removing tank, ceramic ring filtering system and alkali sprayers), which will guarantee safety, energy saving and no pollution in the conversion of plastic waste to fuel oil process.
3. High oil output rate
On the one hand, the mechanical conversion of plastic into fuel is equipped with tubular condenser which has larger cooling area and better cooling effect. On the other hand, the catalyst we use is made of 24 kinds of chemicals, which can improve oil yield as well as guarantee the oil quality. With the two special methods, we can guarantee the average oil output rate as high as 55%.
The mechanical conversion of plastic into fuel has introduced the newest pyrolysis technology, which can convert waste plastic to oil, carbon black and a little combustible gas. All the final products are very useful and have wide applications. By investing in the plastic recycling pyrolysis plant, our customers can profit much from processing waste plastics; at the same time, it can also reduce waste plastic pollution as well as make contribution to the environment.
2. Safe and environment friendly
The mechanical conversion of plastic into fuel is equipped with mature safety devices (alarm for over temperature and pressure, auto pressure releasing system, extra gas recycling system, fire fighting devices) and advanced dedusting system (dust chemical removing tank, ceramic ring filtering system and alkali sprayers), which will guarantee safety, energy saving and no pollution in the conversion of plastic waste to fuel oil process.
3. High oil output rate
On the one hand, the mechanical conversion of plastic into fuel is equipped with tubular condenser which has larger cooling area and better cooling effect. On the other hand, the catalyst we use is made of 24 kinds of chemicals, which can improve oil yield as well as guarantee the oil quality. With the two special methods, we can guarantee the average oil output rate as high as 55%.
Technical parameter of Mechanical conversion of plastic into fuel | ||||
No. | Items | Contents | ||
1 | Equipment type | DY-1-6 | DY-1-8 | DY-1-10 |
2 | Raw material | Waste plastic | Waste plastic | Waste plastic |
3 | Structural form | Horizontal rotation | Horizontal rotation | Horizontal rotation |
4 | 24-hour Capacity | 6 ton | 8 ton | 10 ton |
5 | Oil yield | 2.7-3.3ton | 3.6 -4.4ton | 4.5 -5.5ton |
6 | Operating pressure | Normal | Normal | Normal |
7 | Material of pyrolysis Reactor | Q245R | Q245R | Q245R |
8 | Thickness of pyrolysis Reactor | 16mm | 16mm | 16mm |
9 | Rotate speed of pyrolysis Reactor | 0.4turn/minute | 0.4turn/minute | 0.4turn/minute |
10 | Total power | 19KW | 19KW | 19KW |
11 | Mode of cooling | Water cooling | Water cooling | Water cooling |
12 | Cooling area of condenser | 100sqm | 100sqm | 100sqm |
13 | Kind of transmission | Internal gear drive | Internal gear drive | Internal gear drive |
14 | Noise dB(A) | ≤85 | ≤85 | ≤85 |
15 | Size of Reactor(D×L) | 2200×6000 | 2200×6600 | 2600×6600 |
16 | Working form | Intermittent operation | Intermittent operation | Intermittent operation |
17 | Delivery time | 20days | 20days | 20days |
18 | Weight | 27T | 30T | 35T |
Prepared by customer about Mechanical conversion of plastic into fuel | |||
No. | Item | Consumption | |
1 | Coal(for choice) | 500kg/day | |
2 | Wood(for choice) | 800kg/day | |
3 | Natural gas(for choice) | 100-150kg/day | |
4 | Oil(for choice) | 300-350kg/day | |
5 | Electricity | 244kwh/day | |
6 | Water(recycled) | 60㎥ /month | |
7 | Total power | 19kw | |
8 | Land area | 35m*15m |
Mechanical conversion of plastic into fuel final product
Fuel Oil (40% to 45%)
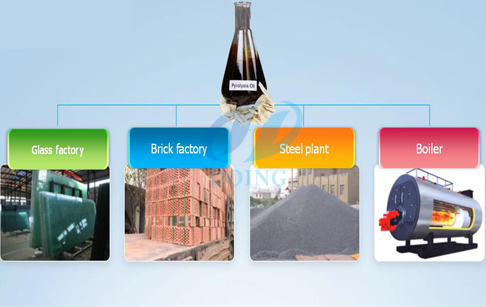
Fuel oil application
The main oil product produced by our recycling application is the fuel oil that is wide used for industrial and commercial purposes. The oil has 40% to 45% of the amount of recycled scrap tyres, which will be carried with licensed tanker trucks.
Carbon Black Powder (30% to 35%)
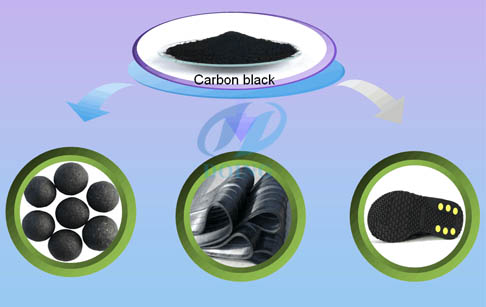
Carbon black application
The second product of mechanical conversion of plastic into fuel is carbon black. The quantity of carbon black is about 30% to 35% according to tyre quality. The use of carbon black is as a chemical strengthener in rubber and coloring agent in pigment industries. This carbon black price is very competitive compare to petroleum carbon black, so our pyrolysis carbon black is good option in stead of petroleum carbon black.
Pyrolytic Gases ( About 10 % )
We get pyrolytic gases during process about 10% of waste tyre. The main component of this gases are methane ( CH4 ), so we can not condense and store this gases. We use this gases to heat the reactor and we can use exceed gases for other heating application.
Request Information
Send your inquiry for further information