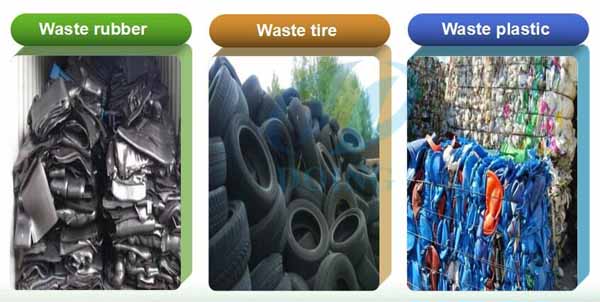
Waste tire /plastic
Waste plastic disposal is a serious social problem since it’s very difficult to decompose, which is called ”white pollution”.Waste tire is often called “black pollution”,they not only easily causes fire, but also pollutes the environment.Henan Doing produced used tire/plastic to oil processing plant is a green technology which can not only process waste plastic/tire zero pollution but also change the waste plastic/tire into fortune.
Used tire/plastic to oil processing plant
The used tire/plastic to oil processing plant is a green technology to solve tire/plastic and other environment pollution which are becoming the serious issues nowadays and it is the meaningful industry. The tire/plastic pyrolysis oil, one kind of end products extracted from the pyrolysis process, is often used for producing heat, electricity, steam and so on.
Used tire/plastic to oil processing plant working process
Used tire/plastic to oil processing plant working process
Put 10 tons waste tire/plastic into reactor after necessary decontamination processing and simple cutting, then close the door. Heat the reactor with wood, coal, oil or gas.
When temperature reaches 100 degrees, pyrolysis starts in the reactor. And oil gas comes out from oil outlet.
When oil gas from reactor goes through catalyst chamber, top cooling pipe, oil- waster separator, heavy oil is collected in the heavy oil tank. Other oil gas continue to go through high-power cooling system ( horizontal condenser) and cooling down , finally collect into the light oil tank. Uncondensable gas can be recycled to heat the pyrolysis machine reactor.
When all the oil gas is extracted out, only carbon black and steel wire left in the reactor. After reactor cooling down, carbon black and steel wire slagging out automatically. Steel wire can be sold directly in the market to the steel factory.
After process with a magnetic separator, carbon black mix with organic chemical adhesive can be used to make coal briquette. The calorific value reach to 6000 calories. It is a very good energy used to heat the reactor instead of wood , coal, gas, fuel.
Used tire/plastic to oil processing plant feature
1. Unique design of reactor guarantees the service life and safety.
2. No need to crush tires. We can feed whole tires into the reactor. Save manpower and increase efficiency.
3. Electric cabinet help you watch the temperature and easy to control power.
4. Technical condensers and circulating water guarantee the cooling effect and improve oil yield.
5. The residual gas (tail gas) recycles to furnace as fuel. Save energy.
6. Flue gas is processed by dust removal device. Reach the emission standard.
7. Experienced engineers will help you install the machine and train your workers.
Used tire/plastic to oil processing plant has two important parts
Used tire/plastic to oil process plant
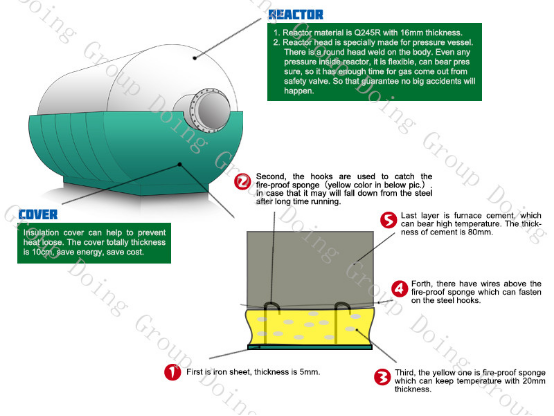
Used tire/plastic to oil process plant reactor
Used tire/plastic to oil processing plant has two important parts, reactor and condensers.
The reactor decides the whole machine’s service life. In the refining industry, when heating the reactor by fuel, the heating temperature can be up to 450—500 degree centigrade inside the reactor. Our 5th generation machines use the Q245R boiler steel plate as material, it stresses on the high temperature and high pressure resistant, and its melting point can reach to 800 degree centigrade, which can assure 6-8 year’s lives and it conform to the national standard.
Meanwhile, all machine parts are welded with auto-welding machine, pressure parts will be 100% X-ray detection, heat treatment and hydra press measurement, safety assurance.