Continuous process of plastic into oil machine
Continuous process of plastic into oil machine of technologies aims to present an overview of the technologies available for converting waste plastics into a resource. It emphasizes the typical methods for converting waste plastics into solid, liquid a nd gaseous fuels as well as the di rectcombustion of waste plastics for specific applications.
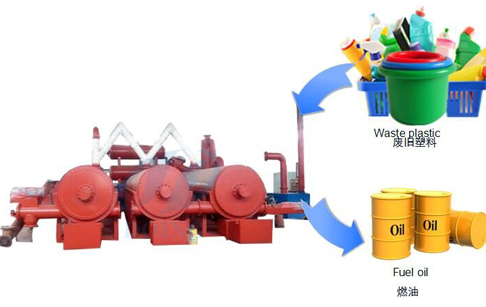
Continuous process of plastic into oil machine
With the moderation of the society, plastic industry develops at a rapid speed, plastic manufactures are widely used in many field of life. The pollutant of plastic, increasing for its difficulty in decomposing; which was called “White pollution”, has became a big threat to the environment and get increasingly serious. Compared to the developed countries, we are still lack of experiences in treating the pollution; the capital and market are also big problems.
Henan Doing produced continuous process of plastic into oil machine,the machine can convert waste plastic into oil and carbon black,the plastic oil and carbon black can bright huge profit for you.
Continuous process of plastic into oil machine have many advantages:
1.Fully automatic with low labour cost
Our continuous process of plastic into oil machine is controled by PLC system with automatic feeding and discharge system, which only need 1-2 worker for operating the PLC or computer is ok.
2.Fully pyrolysis for high oil output
Our continuous process of plastic into oil machine adopts mutiple reactor design which can make fully pyrolysis of waste tires, thus to get high oil output.
3.Big capacity
Also due to continuous feeding and discharge system, and unique mutiple reactor design, our fContinuous process of plastic into oil machine can process at least 10 tons waste plastices per day, up to 100T/D.
4.Internal rotating for conitnuous operation
For external rotating system, you have to change the sealing material every three days, thus cannot achieve the real sense of continuous process. But our continuous process of plastic into oil machine pyrolysis reactor adopts internal rotating method, which no need to worry about the sealing of the external rotating system.
5.Continuous working save time and energy
6.Long working life
During the continuous pyrolysis process, reactor heating is by indirect hot air heating, which will not damage reactor so much, thus to keep long usage life of the reactors.
Continuous process of plastic into oil machine technical data
Continuous process of plastic into oil machine final product application
Pyrolysis oil :- 40 to 45%
Carbon black:- 30 to 35%
Pyrolysis Gas:- About 10 %
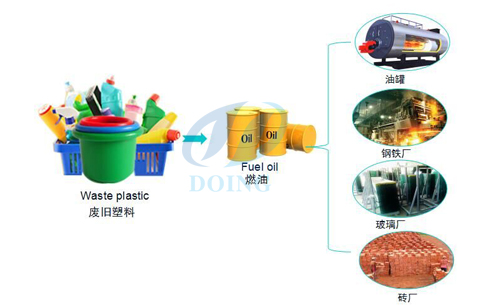
Fuel oil usage
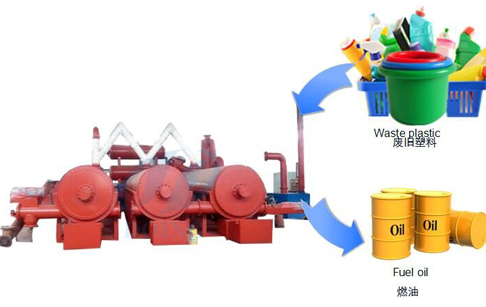
Continuous process of plastic into oil machine
Henan Doing produced continuous process of plastic into oil machine,the machine can convert waste plastic into oil and carbon black,the plastic oil and carbon black can bright huge profit for you.
Continuous process of plastic into oil machine have many advantages:

Our continuous process of plastic into oil machine is controled by PLC system with automatic feeding and discharge system, which only need 1-2 worker for operating the PLC or computer is ok.
2.Fully pyrolysis for high oil output
Our continuous process of plastic into oil machine adopts mutiple reactor design which can make fully pyrolysis of waste tires, thus to get high oil output.
3.Big capacity
Also due to continuous feeding and discharge system, and unique mutiple reactor design, our fContinuous process of plastic into oil machine can process at least 10 tons waste plastices per day, up to 100T/D.
4.Internal rotating for conitnuous operation
For external rotating system, you have to change the sealing material every three days, thus cannot achieve the real sense of continuous process. But our continuous process of plastic into oil machine pyrolysis reactor adopts internal rotating method, which no need to worry about the sealing of the external rotating system.
5.Continuous working save time and energy
6.Long working life
During the continuous pyrolysis process, reactor heating is by indirect hot air heating, which will not damage reactor so much, thus to keep long usage life of the reactors.
Continuous process of plastic into oil machine technical data
No. | Item | Specifications | ||||||
1 | Model | DY-C-10 | DY-C-20 | DY-C-30 | DY-C-50 | DY-C-60 | DY-C-80 | DY-C-100 |
2 | Cpacity | 10T/D | 20T/D | 30T/D | 50T/D | 60T/D | 80T/D | 100T/D |
3 | Power | 35Kw | 50Kw | 65Kw | 80Kw | 90Kw | 105Kw | 120Kw |
4 | Working type | Continuous | ||||||
5 | Reactor deisgn | Mutiple reactors (The quantity and size depends on the raw material condition) | ||||||
6 | Rotating | Internal rotating | ||||||
7 | Cooling system | Recycled waster cooling | ||||||
8 | Reactor material | Q245R/Q345R boiler plate | ||||||
9 | Heating method | Indireact hot air heating | ||||||
10 | Heating fuel | Fuel oil/gas | ||||||
11 | Feedstock | Waste tire/plastic/rubber | ||||||
12 | Output | Fuel oil, carbon black |
Continuous process of plastic into oil machine final product application
Pyrolysis oil :- 40 to 45%
Carbon black:- 30 to 35%
Pyrolysis Gas:- About 10 %
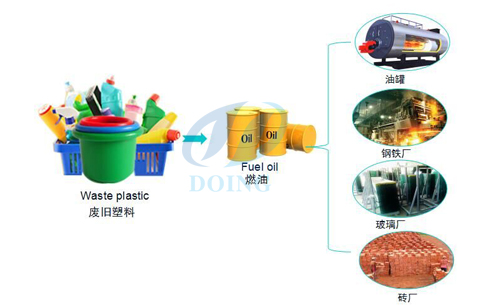
Fuel oil usage
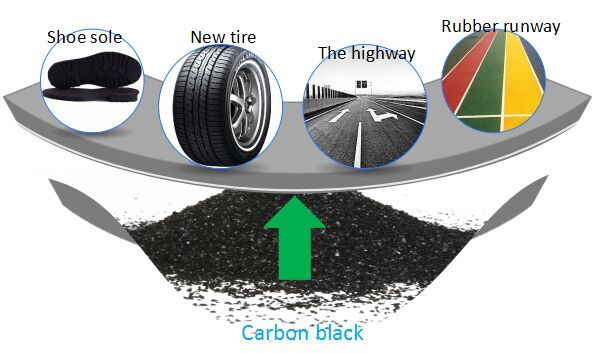
Carbon black usage
Request Information
Send your inquiry for further information