Plastic to fuel conversion process ?
Waste Tire/Plastic Pyrolysis Plant / Date:September 22, 2017
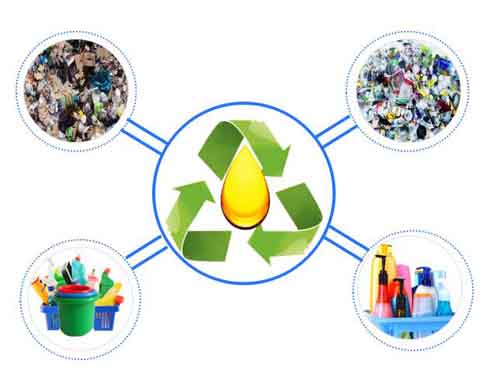
Plastic to fuel conversion process ?
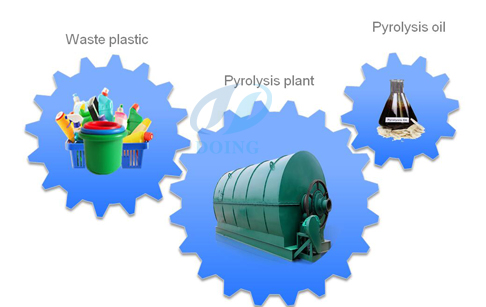
Plastic to fuel conversion process
Plastic to fuel conversion process is an environmental protection system which uses the continuous liquefaction technology and catalytic breakdown reaction to convert waste plastics into renewable resources, such as pyrolysis oil, carbon black, combustible gas and so on. The end products can be applied to diesel engines and generators directly, or come into high ranking diesel and gasoline through our oil refining plant. Other names of convert plastic to oil machine: waste plastic pyrolysis machine, plastic to oil machine/plant, waste plastic to fuel conversion plant, plastic2oil equipment and so on.
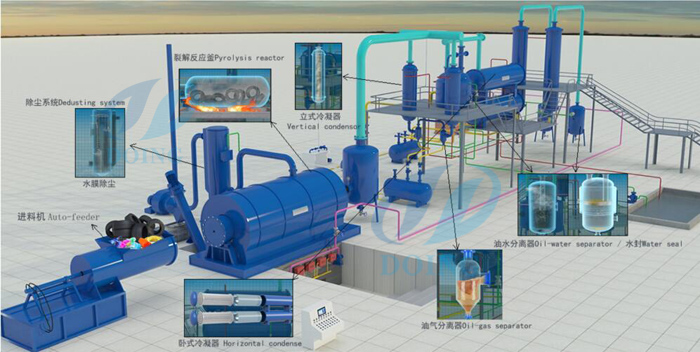
Plastic to fuel conversion process processing waste plastic to fuel
1. Put raw materials into reactor by auto-feeder, then heat the reactor with any one of the following fuel materials: coal, wood, natural gas, oil. Do not stop heating the reactor, when the temperature reaches nearly 250 degree Celsius, waste tyre will be transferred to oil gas.2. The liquid oil will be cooled by condenser from oil gas and then collected by oil tank. Third, the exhaust gas which can not be cooled in normal pressure will be recycled to heat the reactor. In this way, you can not only saving energy, but also protecting environment.
3. Smoke produced by processing the plastics can achieve national emission standard through dual desulfurization and dusting removal device.
4. After you getcrude oil, the temperature will be low, at this time, carbon black will be discharged automatically.
Last, when the temperature falls to 100 degree Celsius, After all these steps, you can start another batch.
Request Information
Send your inquiry for further information